However neutrons and engineering have more in common than you might expect. We take a closer look at ENGIN-X, ISIS Neutron and Muon Source's dedicated engineering beamline, to find out how neutrons have been solving engineering problems for over 20 years.
Measuring stresses and strains at the atomic level
ISIS Neutron and Muon Source produces high energy beams of neutrons that are fired into materials allowing us to study them at the atomic scale. As neutrons don't carry an electrical charge they are largely unaffected by the atoms around them, letting us see deep into materials.
ENGIN-X uses neutrons to non-destructively measure the stresses and strains hidden within engineering components under realistic conditions. Samples can be subjected to stress loads up to 100kN and temperatures up to 1000°C to recreate the challenging conditions engineering components face every day.
Solving engineering problems for more than 20 years
Despite being best known for their science, ISIS Neutron and Muon Source has had a longstanding involvement with engineering. “Not only are a substantial proportion of our workforce engineers, but we have a dedicated instrument that allows us to study engineering components in ways that no other technique can," explains ISIS Neutron and Muon Source director Prof Robert McGreevy.
The use of neutrons to study residual stress was pioneered at the Harwell reactors in the 1970s. ISIS Neutron and Muon Source entered the international stage for engineering stress measurement more than 20 years ago when it built ENGIN - one of the first dedicated neutron stress beamlines in the world. In response to growing demand from the engineering community, ENGIN was superseded by ENGIN-X in 2003, funded by the Engineering and Physical Science Research Council (EPSRC).

Installation of the ENGIN-X guide, which became operational 2003, by the team from Swiss Neutronics. Image credit: ISIS Annual Review 2002.
Prof Robert McGreevy, director of ISIS Neutron and Muon Source adds: “it's great to see such a wide variety of research taking place on ENGIN-X. Not many people realise the important role that neutrons play in engineering, or that engineering plays in neutron research. The social and economic benefits are easy to explain and will continue for many years to come."
Take a look at some of the research that's taken place on this extraordinary instrument below.
Keeping us safe on the move
Neutrons can delve deep into engineering components used in transport such as aircraft wings, jet engine casings and train wheels.
Airbus was able to discover areas of potential stress and weakness in its aircraft wings by testing them using ENGIN-X.
This assures the quality of engineering components before the manufacturing process begins, keeping us safe in the skies. | Image credit: STFC
|
 Image credit: Pixabay
| Surveying stresses and strains in ancient artefacts
Neutrons can be used to non-destructively study ancient artefacts. The facility has previously studied a 3,000 year old vase, bronze age swords, medieval armour, and copper bolts from Napoleonic war era ships. In 2015, ENGIN-X was used to look at a broken ancient tie rod used to support one of the biggest cathedrals in the world – Milan Cathedral.
The experimental data from ENGIN-X revealed the residual stresses in the inner part of the iron rod without damaging the artefact.
|
Stress strain measurements power progress in the energy sector
The energy industry can use neutrons to probe deep into objects of interest. For example, graphite material used in UK nuclear reactors, and materials used in solid oxide fuel cells, have all been examined using ENGIN-X.
The instrument was also used to study pipes for the offshore oil and gas industry. The pipe installation process and welding procedure induce strains in the pipeline which can, in principle, lead to failure.
It is important that pipelines used to carry fluids are robust and able to withstand production and installation. Experimental data from ENGIN-X gave insight into the structural integrity of the pipe during the installation process.
|
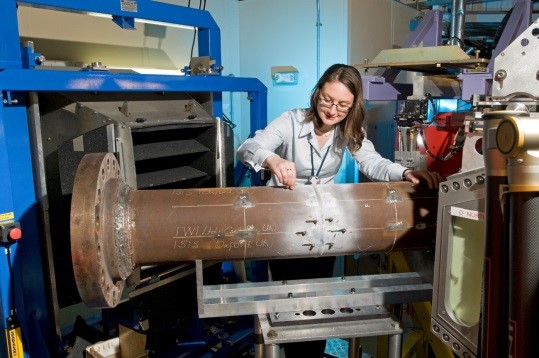 Image credit: STFC
|
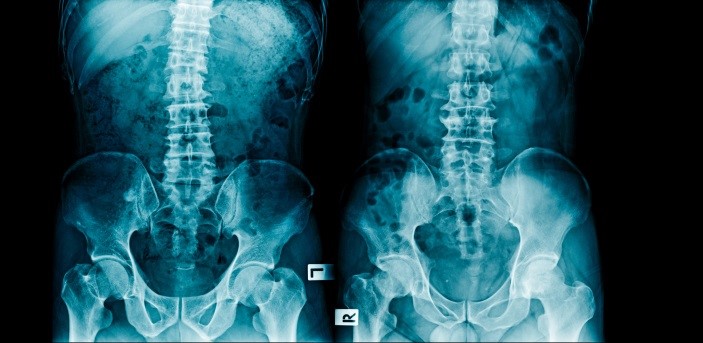 Image credit: Dreamstime
| Monitoring the quality of hip implants
Neutrons can also benefit our health as they can be used to study samples such as orthopaedic implants in great detail. Orthopaedic implants are often coated in a thin layer of hydroxyapatite. The coating process causes stress within the implant, which could cause the implant to fail.ENGIN-X was used to collect stress measurements to determine how the coating process relates to implant failure. Researchers used neutrons rather than x-rays to study the samples as they can penetrate deep into the materials more effectively. Their results were used to develop a computer model used by the implant industry to monitor the quality of hydroxyapatite coatings.
|
Stress test sheds light on solar system formation
Neutrons can also probe samples from the natural world – including meteorites.
ENGIN-X has been used to look at the stresses within samples of meteorites. The type of stress indicates the potential impact and cooling experience it has been through.
These findings could help reveal conditions during the early formation of the solar system.
| Image credit: Pixabay
|
Image credit: Dreamstime
| Solving engineering issues for industry
Over the past 30 years, various industries have directly benefitted from the value that neutron science can bring to their business. ENGIN-X has been used by many companies including EDF Energy, TWI, and Boeing. Researchers from Rolls Royce used ENGIN-X to identify a mechanism they believed led to the formation of surface defects in the turbine blades. The team were able to conclusively identify the mechanism that caused the defects. As a result they've implemented a new manufacturing process that prevents surface defects from occurring. |
Further information