When Polaris beamline scientists Ron Smith and Paul Henry were first approached by a group from Aarhus University interested in studying materials in situ at high temperatures with rapid heating, their initial response was “Yeah, right!" Standard furnace set ups were not capable of the temperatures, or heating rates, required. Luckily, the Danish group were already looking into the feasibility of a furnace to produce similar conditions for the European Spallation Source (ESS). Instead of waiting until the appropriate stage in construction of ESS to build the furnace, the group chose the Polaris beamline at ISIS to develop this idea further.
PhD student Jakob Voldum Ahlburg spent three months at ISIS in early 2018 with the design and preliminary tests, returning in November 2018 for the first in-beam tests. “What makes this furnace different is that it is heated using the principle of induction," he explains; “a water-cooled copper coil generates an oscillating magnetic field and this couples with electrons in the sample tube for quick and efficient heat transfer. Unlike the ISIS standard furnaces, which require their own ultra-high vacuum vessel, the induction furnace can sit directly in the vacuum of the detector tank, reducing background scattering from the sample environment."
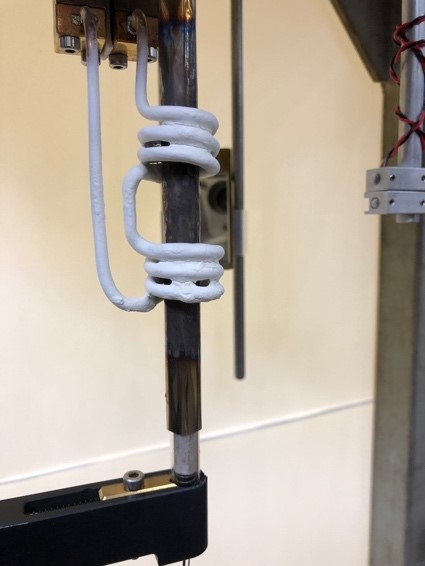
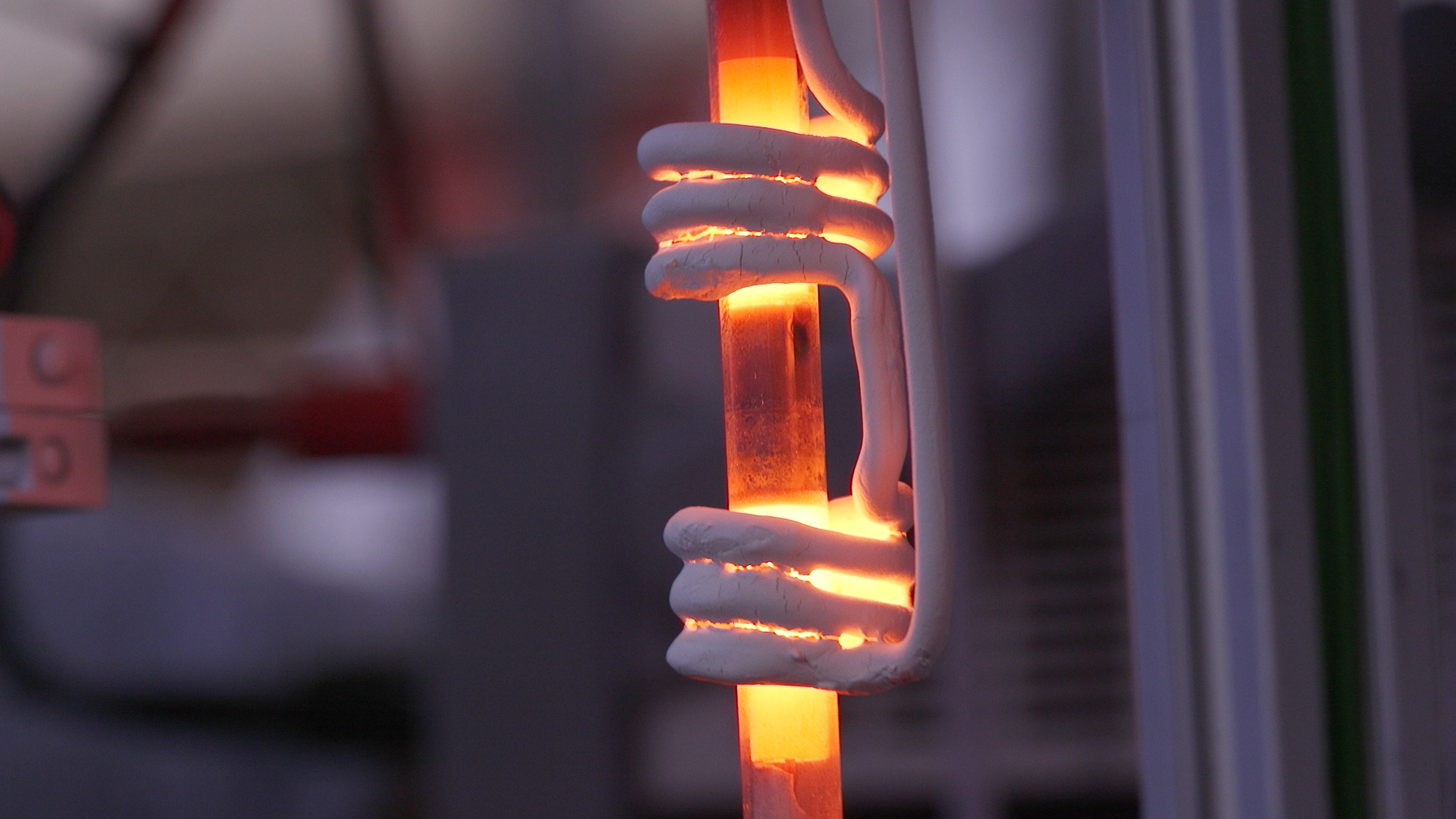
A quartz tube, with a 0.075 mm steel sheet, placed in the centre of the copper coils. The coils are coated with Boron nitride to shield the copper coils from the incident neutron beam.
Induction hobs in new kitchens use similar heating methods, as do those on the Great British Bake Off! Industrial use is widespread, and this is where the group got their inspiration. In the lab in Aarhus, they have achieved sample heating from room temperature to 1400°C within 30 seconds, which is so fast they now face limitations from the thermocouple measuring the temperature. The estimated maximum working temperature of the setup is 1800-2000°C.
However, like most things, it's not that easy once you put a full assembly in a neutron beam! The ideal place for the sample to maximise heating would be inside the coil itself but, unfortunately, this would block part of the incoming and scattered neutron beams. They have designed a furnace where the sample is mounted in a split-coil arrangement and multiple design iterations have successfully maximised the energy transfer from coil to sample. To reduce scattering from the copper coils, the group coated them in boron nitride. In-beam testing revealed application of three coats was sufficient to remove scattering from the coils and their internal water-cooling.
From left to right: Jakob Voldum Ahlburg, Mathias Ibsen Mørch and Frederik Holm Gjørup
The initial in-beam commissioning tests on Polaris using a standard silicon powder enabled investigation of a range of performance parameters such as temperature range; hot-zone stability and gradient; and rate of heating. Incorporation of an optical window and a 45° mirror into the setup allowed a webcam to view the sample in the neutron beam during an experiment.
Many different sample geometries are possible using this furnace, as the coils can be made in different shapes and sizes. The size of the coil also dictates the heating regime: a tighter wound coil will reach higher temperatures, but also have a higher minimum temperature. The testing method allows experimental testing of these different configurations. A long-term objective is adding uniaxial compression, to take measurements during compaction of powders to form dense pellets. This would be the first induction press compatible with neutron scattering experiments.
The group has also been in discussions with other ISIS instrument teams (PEARL and Engin-X) regarding potential applications. The electronics from the Polaris set-up will apply to a range of coil designs that could be used in different neutron experiments, or even in synchrotron environments. As part of their visit to RAL, the Aarhus group will be visiting I11 at Diamond Light Source to see its new furnace, a complementary experimental set up to their new design on Polaris.
Another member of the group, Mathias Ibsen Mørch, is keen for this furnace to be ready for user experiments. He is studying a magnetic ferrite compound that changes phase at 1200°C. So far, he has only been able to perform ex situ experiments, and is unable to probe the effect of cooling rate. An in situ experiment on Polaris would be extremely useful.
Luckily for Ron, Paul, and future users, the group are leaving their furnace on Polaris, but building two copies in Aarhus that they can use for further testing and development; continuing to transfer knowledge between Denmark and ISIS.